Today, mining is no longer the same as it was in the past 10 years. The industry had long depended on slow-moving trucks, manual labor and old conveyor systems. Now, swift hand-offs of resources are changing the way things get done around the world.
Faster delivery of materials, less behind-the-scenes energy use, and added safety are just a few of the many benefits companies reportedly want. They are using modern tools for mining and resources conveying to reach these ends.
Automation to real-time tracking, these enhancements are instrumental. But where are they having the most impact? Below, we review four areas where the efficient movement of resources is revolutionizing the mining landscape.
Tech Is About To Upend The World Of Underground Mining
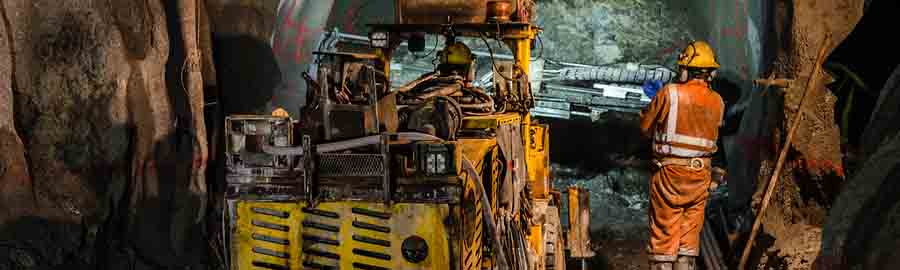
Subterranean mining is a tough business. The spaces are tight. Ventilation is limited. Rock and ore moving from underground is a time-consuming, laborious process. That’s why effective conveyance is particularly important here.
Fancy monitoring also helps. Sensors monitor belt health and monitor load weights in real time. This averts breakdowns and ensures there’s never a pause in production. Some sites have even introduced automation.
Track-bound conveyor lifts are replacing hoists in some mines. These hoists continuously lift drywall, up eliminating, down time. In total, these enhancements help underground mines to operate more quickly, safely, and productively.
Mines Away With Remote, Autonomous Logistics
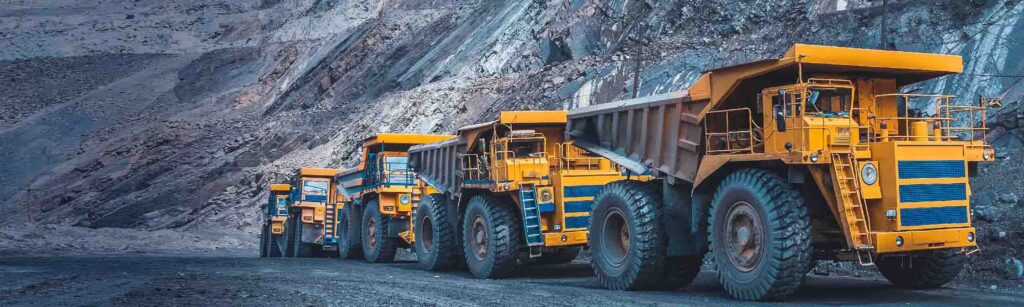
Big challenges await in remote mines. Rough weather, long distances, and bad roads mean that supplies have a hard time getting through. But efficient delivery systems are changing the equation. Trucks drive themselves around the country without drivers and fleets of these trucks go out and deliver materials over great distances. These trucks are powered by electricity or hybrid systems, reducing emissions and increasing reliability.
Drones also aid by scouting routes and conveying tiny tools or samples. They’re not able to carry heavy ore, but they support faster logistical needs and reduce the number of crew required on site. Rail systems are another major win. A small handful of mines have embraced self-driving trains, which transport bulk goods from mines that are often in remote locations, to treatment works or ports.
Even conveyor belts — historically, to be used only on-site — are stretching out. Some now stretch for miles over landscapes, shielded by weatherproof covers. This cuts down on truck traffic and helps materials flow smoothly to processing areas.
Ore Input Left A Lot To Be Desired
The speed and regularity of ore processing plants is emotionally taxing. The raw materials must be delivered just in time. Go too fast and the plant becomes overwhelmed. Too slow, and the production line stops. This is where smart conveyance comes in.
Variable speed belts are employed by the plants of today to adjust input flow with processing capacity. If one segment is running slower, the entire system decelerates in collective rhythm.
Automation is going to take care that every load is weighed, logged, and placed on the right place. Sensors read particle size and ore quality, moment by moment.
That allows operators to quickly configure and adjust sorting and crushing machines. Belts of the mining conveyor system also lead straight into hoppers and crushers, eliminating loaders and manual handling. The second major benefit is in the realm of energy.
Collection: Waste Is Getting Smarter And Greener
Mining generates a great deal of waste — tailings, rock and dust. It’s a big job moving that material efficiently. The old system relied on trucks and manual dumping and wasted fuel while the dumpsters and trucks took up space. These days, many mines have long-distance conveyors that carry waste directly to storage sites.
In some systems, waste is sorted even before it leaves the site. Intelligent conveyors screen out re-usable rock, or break and separate rock at the mine face. This avoids the need for landfilling and creates additional value from byproducts.
Dust control is also an interest. Enclosed conveyors and sprayers can help contain airborne particles when the waste is moved. This makes the air cleaner and shields neighboring communities. Fast waste removal isn’t just about speed — it’s about getting the job done more cleanly and smartly.
Conclusion
Resource conveyancing: Changing the culture of mining from the ground up Smart conveyors are now utilized in plants with underground tunnels. Distance mines depend on the charge fleets.
Automation at processing plants keeps belts smooth. Waste systems are even cleaner and greener. That is a cost-reducing, safer, better-for-environment change.
With new tech continuing to develop, so will the need of intelligent resource movement. In all the four corners of the mining industry, fast reliable material transportation systems are taking the lead.
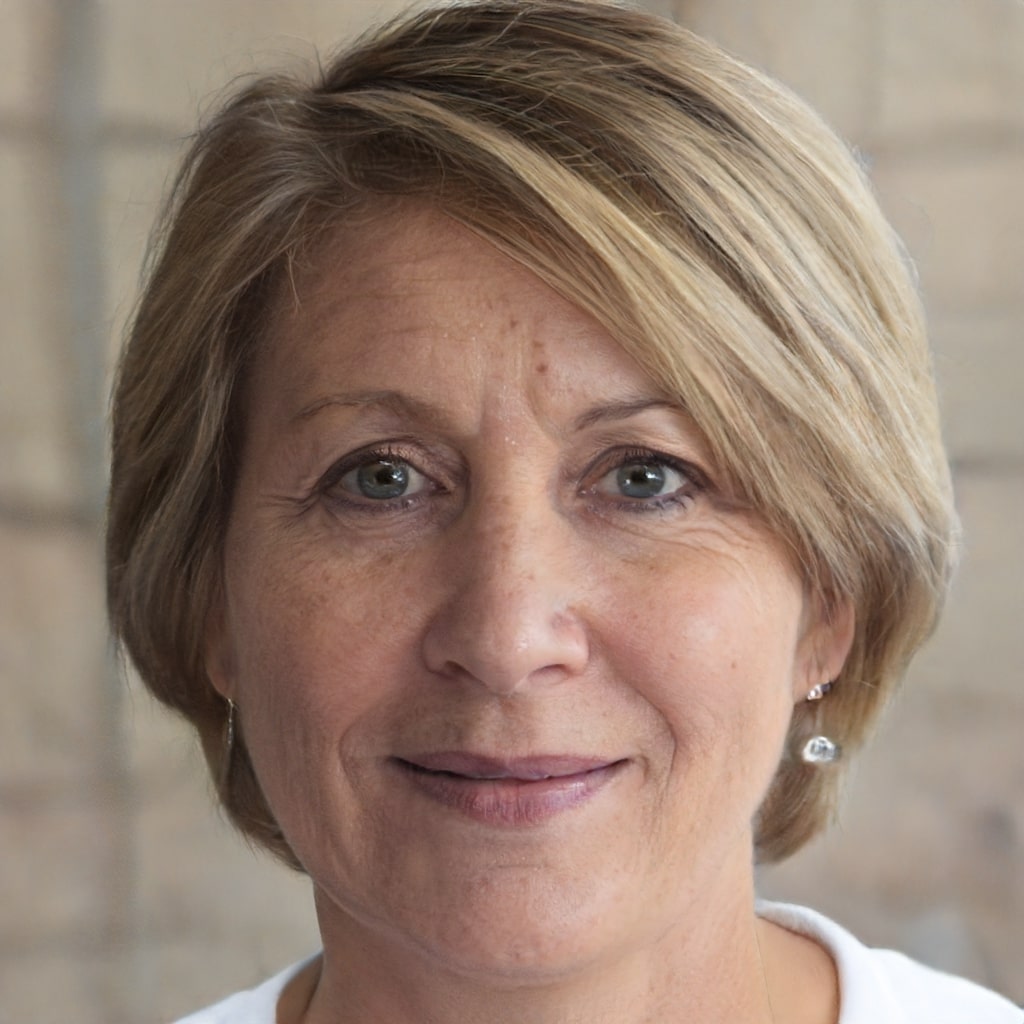